Why is Aluminum preferred over Iron & Steel – And Why PFA’s Outshine SFA’s?
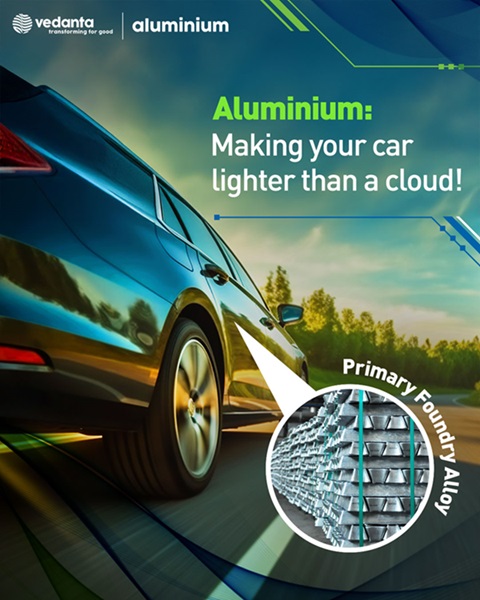
Abstract:Aluminium alloys have revolutionized transportation and automotive industries due to their superior strength-to-weight ratio and excellent corrosion resistance compared to iron and steel. The transition to a greener economy and the rise of electric vehicles (EVs) have amplified the demand for lightweight, fuel-efficient, and sustainable materials. Among these, Primary Foundry Alloys (PFAs) are emerging as the material of choice for critical applications, offering unmatched purity and performance compared to Secondary Foundry Alloys (SFAs).
Technical Explanation
Why is Aluminium replacing Iron & Steel?
The push toward sustainability and energy efficiency is driving the adoption of aluminium alloys over traditional iron and steel:
- Lightweight for Fuel Efficiency: Aluminium’s lightweight properties reduce vehicle weight, significantly improving fuel efficiency in internal combustion engine (ICE) vehicles and enhancing the range of EVs.
- Corrosion Resistance: Aluminium’s natural resistance to rust ensures longer-lasting components, reducing maintenance and lifecycle costs.
- Design Flexibility: Higher silicon content and advanced casting techniques allow aluminium to be used in intricate, high-performance designs.
- Strength-to-Weight Ratio: Aluminium alloys provide comparable strength to steel at a fraction of the weight, making them ideal for lightweight, fuel-efficient transportation solutions.
Applications in the Automotive Industry
Aluminium castings have become integral to automotive engineering:
- Powertrains: Engine blocks, pistons, cylinder heads, manifolds, and transmissions.
- Chassis: Brackets, brake pads, suspension, steering components, and structural panels.
- Body Structures: Doors, bonnets, crossbeams, and other exterior attachments.
- Electric Vehicles (EVs): Battery casings and structural frames.
- Wheels: Cast wheels are a major consumer of aluminium foundry alloys.
PFA vs. SFA – The Key Differentiators
Aspect |
Primary Foundry Alloys (PFAs) |
Secondary Foundry Alloys (SFAs) |
Source |
Pure aluminium with alloying elements. |
Recycled scrap with some primary aluminium added. |
Impurities |
Lower impurity levels (<0.20% Fe for critical applications). |
Higher impurity levels, particularly iron. |
Applications |
Critical components requiring high ductility and strength. |
Non-critical components or pressure die casting. |
Cost |
Higher cost due to purity and production process. |
Lower cost, suitable for less demanding uses. |
Why PFAs Are Preferred
- Purity Matters: Critical applications like alloy wheels, engine block castings require iron levels below 0.20%, achievable only with PFAs.
- Enhanced Mechanical Properties: PFAs exhibit superior ductility, castability, and structural integrity, making them indispensable for stress-bearing automotive components.
- EV Growth Opportunities: As EV production scales, demand for PFAs in structural and battery components is set to rise due to their lower impurity levels and superior performance.
Easy example for better Understanding
Imagine building a house. You could use bricks made from pure, high-quality clay (PFAs) or bricks made from recycled materials mixed with impurities (SFAs). The pure clay bricks are stronger, more uniform, and better suited for critical parts of the house like the foundation or load-bearing walls. They ensure the house stands firm and lasts long.
On the other hand, the recycled bricks might be cheaper and okay for building a garden wall or a tool shed but aren’t reliable for the main structure because impurities can weaken them. Similarly, PFAs are the reliable choice for critical, high-performance auto parts, while SFAs are suited for simpler, less demanding applications.