WARNING: Your Home’s Fire Safety System Could Be a Ticking Time Bomb!
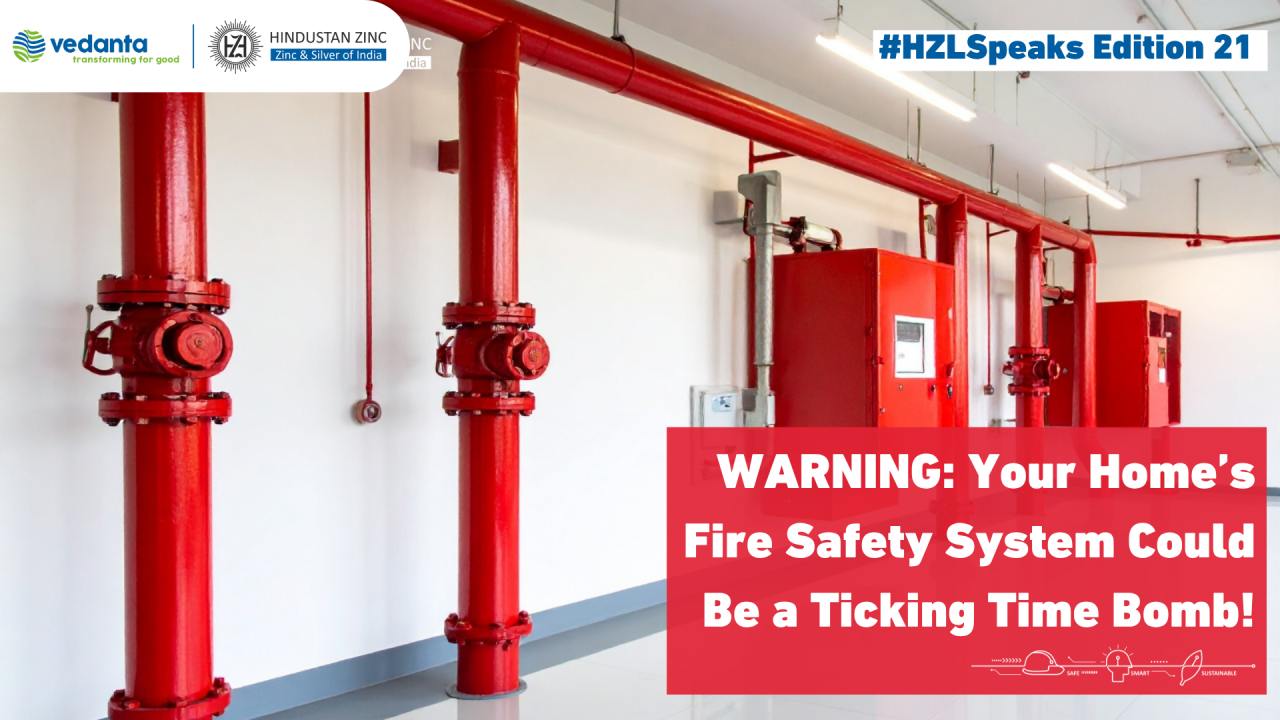
WARNING: Your Home’s Fire Safety System Could Be a Ticking Time Bomb!
Imagine spending a quiet evening at home when a tiny spark suddenly transforms into a raging inferno, endangering your loved ones and everything you hold dear. For many Indian households, this is not a far-fetched horror story – it’s a potential reality if our fire safety systems are compromised by substandard components. In a nation like India, where rapid urbanization and evolving building practices are the norm, neglecting proper fire safety equipment can have catastrophic consequences. This frightening thought should prompt every homeowner to closely examine the critical components that protect their property.
One of the most critical yet frequently overlooked elements in fire protection is the type of pipes used in these systems. Conventional black pipes, made from non-galvanized, uncoated steel, are highly vulnerable to rust. Over time, this corrosion can lead to ruptures and clogging, thereby crippling the efficacy of fire safety systems when they are needed the most. More alarmingly, when rusted pipes in fire-retardant or HVAC systems come into contact with aluminium and oxygen in high-temperature conditions, they can trigger a thermite reaction. This highly exothermic reaction intensifies the fire, dramatically increasing the risk to both property and life.
In stark contrast, galvanized iron (GI) pipes emerge as an undisputed superior alternative. Treated with a robust zinc coating through hot dip galvanizing, these pipes are not only shielded from rust and corrosion but also demonstrate unmatched mechanical durability. This protective zinc coating ensures that the pipes maintain their integrity even in the harshest environments. The robustness of GI pipes makes them a reliable, long-term solution for fire safety systems, requiring zero maintenance over a span of 25 years. On the other hand, painted pipes can cost up to 200% above their initial price over the same period due to ongoing maintenance and repainting needs.
Beyond their economic benefits, GI pipes offer enhanced reliability in maintaining the integrity of fire safety systems. Their resistance to environmental wear and mechanical damage – during erection, dismantling, use, handling, and transportation – ensures that the fire safety infrastructure remains robust even under stress. This resilience is vital for safeguarding not only buildings but also the lives of those who reside in them.
It is crucial for homeowners, builders, and facility managers to recognize that investing in high-quality fire safety components is more than just a regulatory requirement – it is a proactive measure to protect lives, property, and the environment. The decision to use GI pipes can be the defining factor between a controlled emergency and a devastating disaster.
Don’t wait until it’s too late. Take a closer look at your current fire safety systems, consult with experts, and upgrade to galvanized iron pipes. Every detail counts when safeguarding what matters most. Remember, choosing GI pipes isn’t just a purchase – it’s a smart, long-term investment in a safer future for you and your loved ones.
Your Car Could Be Rusting Right Now, And This Monsoon Will Make It Worse!
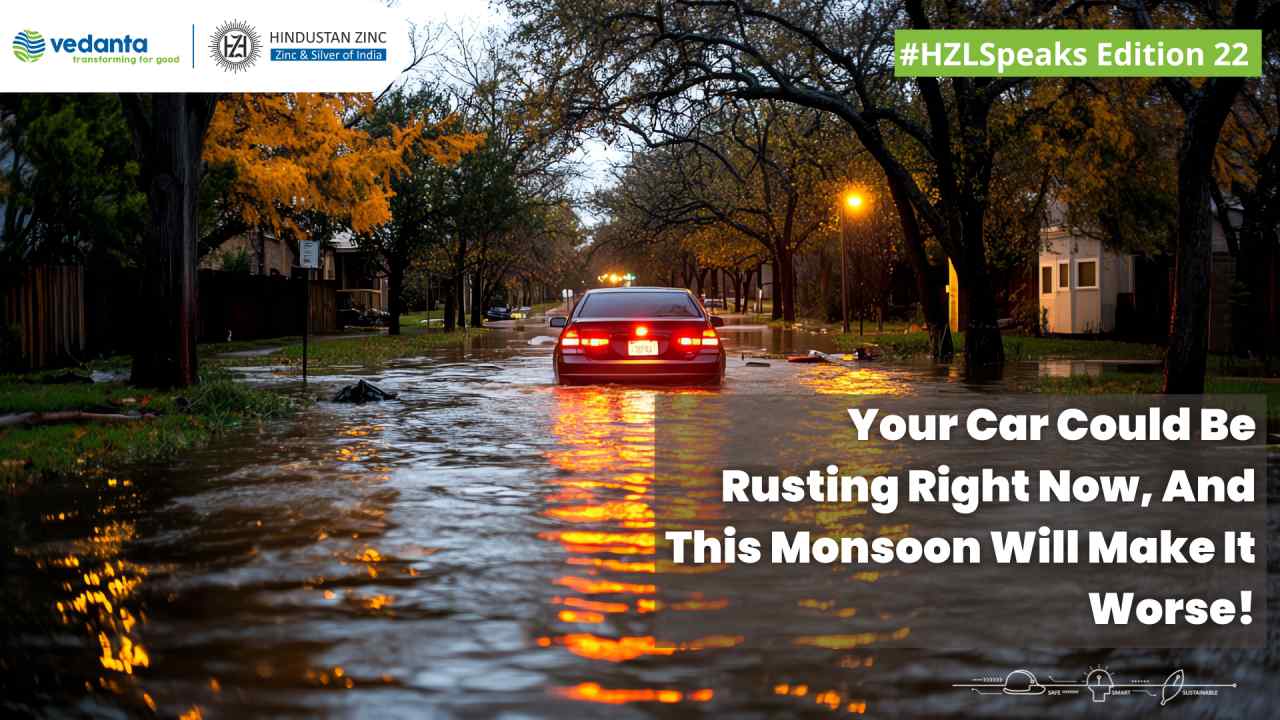
Your Car Could Be Rusting Right Now, And This Monsoon Will Make It Worse!
Would you buy a car with premium interiors, hi-tech features, and a rusting skeleton? That’s the hidden trade-off most Indian car buyers unknowingly make every day. While Indian consumers splurge on sunroofs, infotainment systems, and alloy wheels, the car’s core – the steel body, often lacks the basic protection it needs to withstand India’s punishing weather.
With over 380 million registered vehicles on Indian roads and counting, corrosion is quietly shortening vehicle lifespans, raising maintenance costs, and undermining resale values. Most buyers don’t realize that over 70% of a car is steel, and without proper protection, steel rusts fast, especially in India’s humid, coastal, and rain-soaked conditions.
Now here’s the shocker: while 80% of cars made for export in India are zinc-galvanized, protecting them against corrosion, less than 25% of cars sold within India receive the same treatment. This means Indian buyers are paying global prices but getting second-tier protection.
Zinc galvanization, a process where steel is coated with zinc, offers powerful, long-term defense. The zinc not only forms a barrier but also sacrifices itself to shield the steel (cathodic protection), even when scratched. It boosts the car’s crash strength, reduces maintenance, and protects against rust—rain or shine.
A study by IIT Bombay and the International Zinc Association found that non-galvanized vehicles experience up to 65% corrosion in just five years, compared to only 7% in galvanized ones. And yet, anti-rust warranties are almost non-existent in India.
Painted bodies chip. Coatings peel. Rust creeps in. The cost to galvanize? Just 0.1% of a car’s price, a tiny investment for a longer-lasting, safer vehicle. It reduces repairs, preserves resale value, and ensures your car doesn’t fall apart from the inside out.
This monsoon, ask one powerful question before buying: “Is this car galvanized?”
As India rises as a global automotive force and zinc demand is projected to grow 22% by 2030, it’s time for carmakers to prioritize longevity, not just looks.
Because your car isn’t just a ride, it’s a long-term investment. And without zinc, it’s an investment that could literally rot away.
Hindustan Zinc Ushers in an Era of Online Metal Buying via Digital Auctions
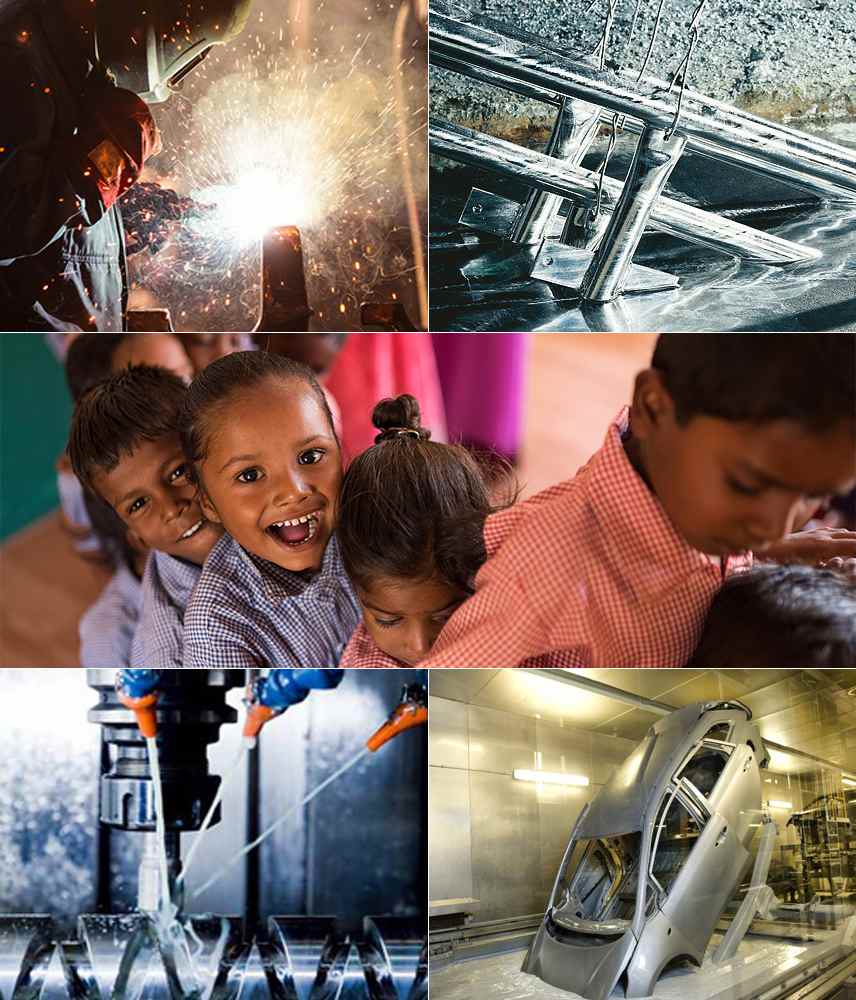
Hindustan Zinc Ushers in an Era of Online Metal Buying via Digital Auctions
Hindustan Zinc Limited (NSE: HINDZINC), India’s only and the world’s largest integrated zinc producer, is redefining the metal procurement experience through its transformative Online Price Discovery (OPD) and Digital Pricing Automation platforms. Integrated into the state-of-the-art Vedanta Metal Bazaar, these pioneering digital initiatives aim to bring the seamless, transparent experience of B2C e-commerce to the traditionally complex world of metal procurement. With 100% of its zinc, lead and silver portfolio now available through real-time, transparent online auctions, Hindustan Zinc is setting a new industry standard by offering customers unparalleled accessibility, flexibility and control while delivering a seamless experience even amid fluctuating commodity prices.
All of Hindustan Zinc’s products are now offered through online auctions. The dynamic pricing model enables real-time digital transactions, allowing businesses of all sizes — from MSMEs to large industrial enterprises — to discover market-driven prices for premium-quality zinc and lead. The company’s offering includes London Metal Exchange (LME)-registered world-class products such as Special High-Grade (SHG) Zinc, High-Grade (HG) Zinc, Asia’s first low-carbon ‘green’ zinc EcoZen, Prime Western (PW) Zinc, Continuous Galvanizing Grade (CGG) Zinc, Special High-Grade Jumbo Zinc, High-Grade Jumbo Zinc, Hindustan Zinc Die Casting Alloys 3 and 5, Special High-Grade Lead, as well as London Bullion Market Association (LBMA)-registered silver bars (30 kg and 1 kg) and Silver Powder, among other variants. As a fully integrated mine-to-metal producer, Hindustan Zinc ensures a reliable supply chain, guaranteeing uninterrupted delivery of critical metals to global markets.
Zinc plays a crucial role in galvanization, protecting steel from rust, making it indispensable for industries such as infrastructure, automotive, renewable energy, electronics, hi-tech manufacturing, defence and electric mobility. Lead is essential for use in automotive batteries, defence, construction, pigments, cable sheathing and radiation protection. Meanwhile, industrialization has propelled silver into a pivotal role across sectors such as high-end electronics, artificial intelligence, nanotechnology and biotechnology.
Traditionally, procuring zinc and lead involved constant price monitoring, manual financial reconciliation and logistical complexities, often impacted by geopolitical disruptions and supply chain constraints. The digitalization of the metal procurement process provides a streamlined, digital-first solution that enables businesses to procure metals efficiently and cost-effectively. The platform supports a digitally traceable experience from quotation to confirmation, providing total transparency and operational efficiency. Fully integrated with global commodity exchanges such as the LME and foreign exchange markets, the system ensures prices remain aligned with international benchmarks. Auctions are run during LME trading hours, extending accessibility beyond standard business hours. Even small-volume buyers benefit from transparent pricing, enabling MSMEs to make purchases at the most opportune time.
Customers can now execute spot or long-term contracts with just a few clicks. This platform now introduces global-standard features such as on-the-spot screen pricing, on-the-spot target pricing based on predefined criteria in addition to long-term contracts. Seamless integration with world-class systems ensures fluid data movement across pricing, finance and sales functions. Built-in margin controls and risk mitigation mechanisms support agile, informed decision-making across the value chain. These features reflect a customer-first approach, supported by Hindustan Zinc’s Customer Technical Services team, which works closely with customers to ensure a seamless buying experience.
Sharing his thoughts, Mr. Arun Misra, CEO – Hindustan Zinc, said, “Metals are the core of India’s economic progress, enabling industries that shape our nation’s future. At Hindustan Zinc, we believe that collaborating with customers and offering them best-in-class services is key to driving this progress. With our pioneering Online Price Discovery and Digital Pricing Automation platforms we are placing the control directly in the hands of our customers thereby democratizing access to critical resources.”
Speaking about the digital experience, Hindustan Zinc’s esteemed customer Mr. Lalit Shah from Mahaveer Metals said, “Vedanta Metal Bazaar has truly transformed the way we engage with metal procurement. The platform is intuitive, transparent and designed with the customer in mind — from live LME pricing to seamless bidding processes, every aspect empowers businesses like ours to make smarter, faster decisions. What once required cumbersome processes is now available at our fingertips through digital platforms, giving us greater visibility, control and confidence.”
Hindustan Zinc offers one of the world’s largest zinc product portfolios, supplying to over 40 countries with a strong focus on customer innovation. Further strengthening the supply chain is Zinc Freight Bazaar, a digital-first logistics platform offers features such as live shipment tracking, route planning, bidding tools and a network of affiliated logistics partners. Hindustan Zinc’s products are the first in India to be Environmental Product Declaration (EPD) verified and are certified by BIS (Bureau of Indian Standards) for quality. Additionally, the company also has REACH quality certification for exporting its products to Europe.
Hindustan Zinc Limited, a Vedanta Group company, is the world’s largest integrated zinc producer and is amongst the top 5 silver producers globally. The company supplies to more than 40 countries and holds a market share of about 77% of the primary zinc market in India. Hindustan Zinc has been recognized as the world’s most sustainable company in the metals and mining category for the second consecutive year by the S&P Global Corporate Sustainability Assessment 2024.
About Hindustan Zinc Limited
Hindustan Zinc Limited (BSE: 500188 and NSE: HINDZINC), a Vedanta Group company, is the world’s largest integrated zinc producer and the third-largest silver producer. The company supplies to more than 40 countries and holds a market share of about 75% of the primary zinc market in India. Hindustan Zinc has been recognized as the world’s most sustainable company in the metals and mining category for the second consecutive year by the S&P Global Corporate Sustainability Assessment 2024, reflecting its operational excellence, innovation, and leading ESG practices. The company also launched EcoZen, Asia’s first low carbon ‘green’ zinc brand. Produced using renewable energy, EcoZen has a carbon footprint of less than 1 tonne of carbon equivalent per tonne of zinc produced, about 75% lower than the global average. Hindustan Zinc is also a certified 2.41 times Water-Positive company and is committed to achieving Net Zero emissions by 2050 or sooner. Transforming the lives of 1.9 million people through its focused social welfare initiatives, Hindustan Zinc is among the Top 10 CSR companies in India. As an energy transition metals company, Hindustan Zinc is pivotal in providing critical metals essential for a sustainable future.
Learn more about Hindustan Zinc on – https://www.hzlindia.com/home/ and follow us on LinkedIn, Twitter, Facebook, and Instagram for more updates
Zinc vs. Time: The Battle Against Corrosion – and Zinc Always Wins!
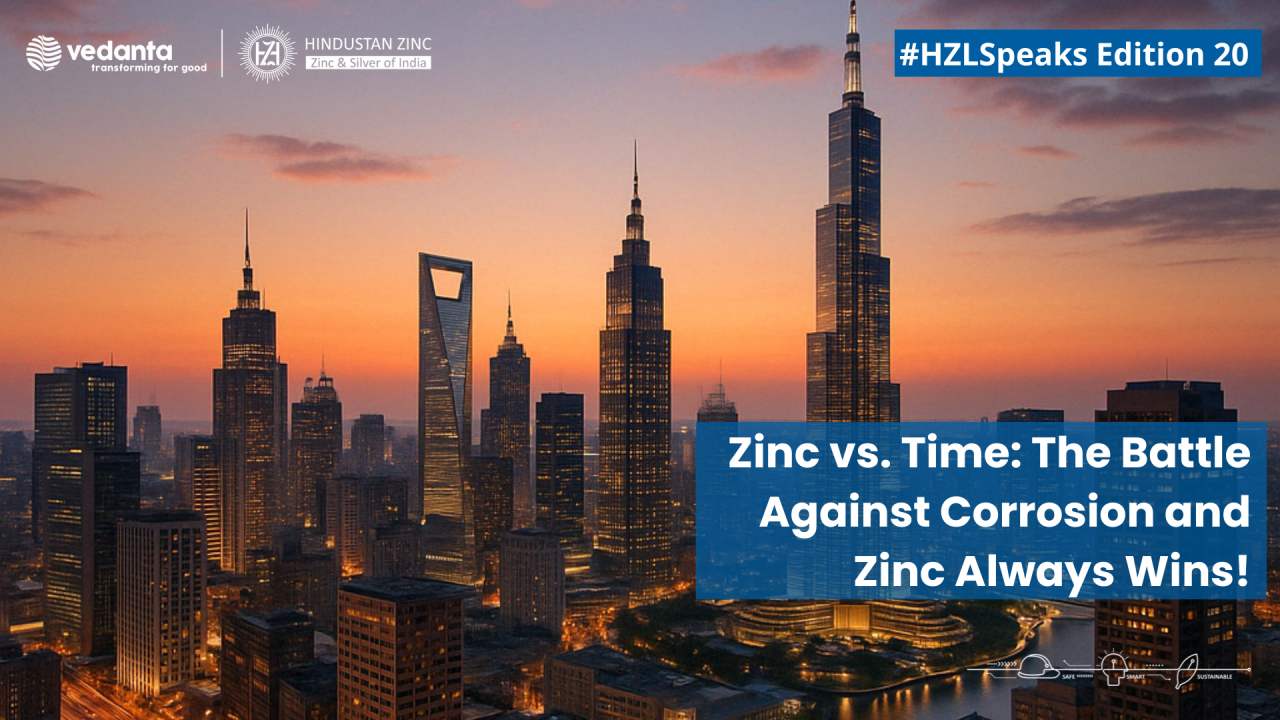
Zinc vs. Time: The Battle Against Corrosion – and Zinc Always Wins!
Dear Readers,
Do you know? Corrosion is a prominent destroyer, eating away at infrastructure and costing India a staggering 5% of its GDP annually. It weakens bridges, buildings, and railways – turning steel into dust. But what if there was a way to defy time and nature? Enter zinc – the ultimate shield against corrosion. With Hindustan Zinc as the world’s largest integrated zinc producer, India has the power to revolutionize infrastructure with this #MetalForLife.
In this edition of #HZLSpeaks, we unveil how zinc is fortifying India’s progress and accelerating its journey to a $5 trillion economy. Corrosion is relentless, but zinc fights back – offering unmatched protection through galvanization. It involves coating steel with a protective layer of zinc, which prevents rust and extends the lifespan of structures. This significantly reduces recurring inspection and maintenance costs, saving India crores in infrastructure expenses. Zinc plays a pivotal role in safeguarding public infrastructure, residential buildings, railways, roads, bridges, and power transmission networks. Unlike paint or anti-rust treatments that wear off, zinc sacrifices itself to protect steel, forming an impenetrable barrier against rust. The result? 50+ years of durability with little to no maintenance.
From towering skyscrapers to intricate bridges, zinc stands tall behind India’s architectural icons – Pradhanmantri Sangrahalaya, Lotus Temple, YashoBhoomi, Nau Sena Bhawan and even global marvels like Burj Khalifa and Lusail Stadium.
With infrastructure booming and zinc consumption set to surpass 2 million tonnes, this metal is more than just a protector – it’s a catalyst for India’s transformation. As the nation builds smarter, stronger, and more sustainable, zinc will be at the heart of it all. Stay tuned as Hindustan Zinc’s #MetalsForLife continue to fuel India’s #AmaZinc infrastructure revolution.
#ZincForLife #SustainableInfrastructure #MakeInIndia #HZLSpeaks
Al-59 Alloy Ingot: Vedanta Aluminium – Engineering Excellence in the Melt
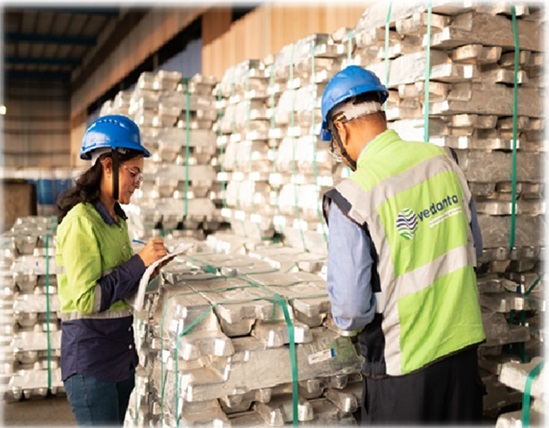
Al-59 Alloy Ingot: Vedanta Aluminium – Engineering Excellence in the Melt
Al-59 Alloy Ingot: Vedanta Aluminium – Engineering Excellence in the Melt
In the rapidly evolving aluminium industry, customer needs and product applications are constantly changing. At Vedanta Aluminium, we pride ourselves on staying ahead by listening to our customers and engineering solutions that not only meet but exceed expectations. One such story of co-creation and innovation is our successful transition from supplying standard P1020 EC ingots to Al-59 alloy ingots — a shift that added significant value for both our customers and our business.
The Challenge: Alloying at Customer End:
Traditionally, we supplied P1020 EC grade aluminium ingots (~99.7% Al) which was used to manufacture EC grade wire rods. However, as market dynamics shifted, demand for Al-59 wire rods began to outpace that of EC (Electrical Conductor) grade rods. To cater to this growing demand, customers must first alloy these EC ingots with silicon and other elements to create Al-59 ingots, which were then cast and rolled into rods.
However, customers soon found themselves struggling with:
- Difficulties in achieving consistent alloying compositions,
- Variation in mechanical and electrical properties of the final wire rods,
- Increased furnace cycle times and energy consumption,
- Higher melt loss and emissions, affecting both cost and sustainability goals.
It became clear: the problem wasn’t in the rod — it started in the melt.
The Metallurgical Science: Silicon’s Silent Power in Al-59:
To understand the magic behind Al-59, we must first understand its core metallurgical principle — the Aluminium-Silicon (Al-Si) binary phase diagram. Al-59 is a hypoeutectic aluminium alloy, typically containing 0.30–0.40% silicon.
The Al-Si phase diagram defines how aluminium behaves when alloyed with varying amounts of silicon:
- Eutectic Point (12.6 wt.% Si at 577°C): At this exact composition and temperature, the alloy undergoes a unique transformation — a liquid phase simultaneously crystallizes into both aluminium and silicon solids.
- Hypoeutectic Alloys (0–12.6 wt.% Si): These are aluminium-rich alloys, like Al-59, which typically contains 0.30–0.40% Si. In such alloys, solidification begins with the formation of primary α-aluminium dendrites, followed by a eutectic mixture.
- Hypereutectic Alloys (>12.6 wt.% Si): These are silicon-rich, where primary silicon crystals form first.
Why Al-59 Works So Well: With its hypoeutectic composition, Al-59 benefits from:
- Enhanced Castability: Silicon addition lowers the melting point, allowing easier and more energy-efficient casting.
- Improved Properties: The formation of fine silicon precipitates within the aluminium matrix increases wear resistance and hardness.
- Dimensional Stability: Superior thermal stability makes Al-59 wire rods reliable in high-temperature and high-stress applications.
In essence, Al-59 strikes the perfect balance — a silicon content low enough to retain aluminium’s ductility but high enough to enhance performance. While in poorly controlled alloying, especially at the customer end, the risk of non-uniform silicon distribution, dendritic segregation, and unpredictable cooling curves significantly leads to wire rods with inconsistent conductivity and properties.
Why This Matters for Wire Rod Applications
Al-59 wire rods are widely used in power transmission cables, automotive harnesses, and conductors exposed to thermal cycling. For such applications, the internal microstructure is critical. Uniform silicon dispersion, fine α-Al grains, and reliable metallurgical bonds ensure that the wire rods can resist deformation during drawing, maintain tensile strength over long spans, and deliver consistent conductivity under load.
The Vedanta Solution: Direct Al-59 Ingot Supply:
Understanding these operational pain points, Vedanta Aluminium stepped in with a holistic, technical solution — supplying Al-59 ingots directly to our customers, eliminating the need for them to carry out alloying at their end. This was a classic case of forward integration with value addition. By offering ready-to-melt Al-59 ingots, we helped streamline our customers’ operations and deliver a more consistent and higher-quality final product.
Why Al-59 Ingots are a Game-Changer – Voice of Customer:
Our customers who transitioned from alloying P1020 to directly using Al-59 ingots have reported transformational benefits across operational, quality, and sustainability metrics:
- 30% Reduction in Furnace Cycle Time: With ready-to-cast Al-59 ingots, customers eliminate the time-consuming alloying step. This leads to faster batch turnaround, boosting throughput without compromising quality.
- Ease of Inventory Management: Instead of stocking multiple elements for alloying, customers manage a single, pre-alloyed ingot — simplifying procurement, storage, and traceability.
- Consistent Quality & Purity: By alloying at our end under controlled conditions, we deliver ingots with strict composition tolerances, uniform microstructures, and predictable performance, batch after batch.
- 20% Fuel Reduction: Less processing means less fuel. By skipping the alloying melt cycle, customers reduce furnace fuel consumption significantly — with immediate impact on efficiency.
- Lower Carbon Emissions: Fuel savings directly translate into reduced emissions. Al-59 enables customers to move towards more sustainable, eco-conscious operations.
- Cost-Effective by Design: Beyond operational gains, Al-59 helps avoid rework, scrap, and hidden inefficiencies — making it a smart choice not just metallurgically, but also financially.
Conclusion:
At Vedanta Aluminium, we don’t just supply metal — we deliver solutions grounded in metallurgy and shaped by customer feedback. Our Al-59 ingot case study is a testament to our customer-first approach and engineering excellence. By transitioning from P1020 EC ingot to Al-59 ingot supply, we enabled smoother production, lower costs, and a greener footprint — all while helping our customers engineer confidence into every cast, every melt, and every meter of wire.
Hindustan Zinc Unveils Digital Zinc Freight Platform
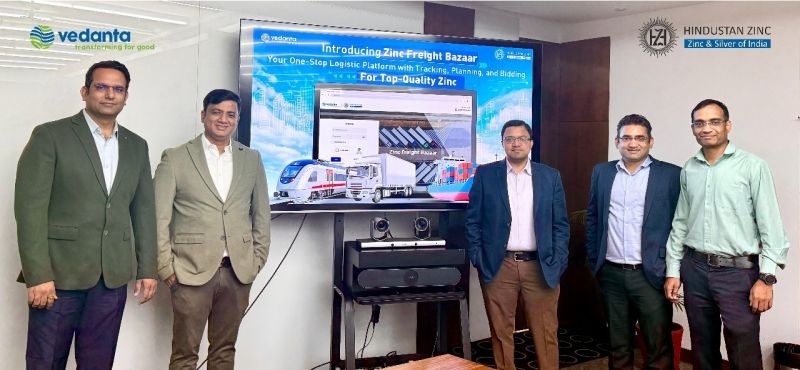
Hindustan Zinc Unveils Digital Zinc Freight Platform
Reimagining logistics, the zinc way.
Introducing Zinc Freight Bazaar – Hindustan Zinc’s digital-first logistics management platform that’s redefining how zinc moves across the nation. From live tracking and bidding tools to a seamless logistics planner, this platform is designed to enhance transparency, simplify procurement, and empower our customers with smarter, faster decisions. As India’s leading integrated zinc producer, we’re proud to be one of the first in the non-ferrous metals sector to roll out such an innovation—marking a bold step toward a future-ready, tech-enabled supply chain.
One platform. Endless efficiency. Welcome to the new age of metal logistics.
A Moment of Global Glory!
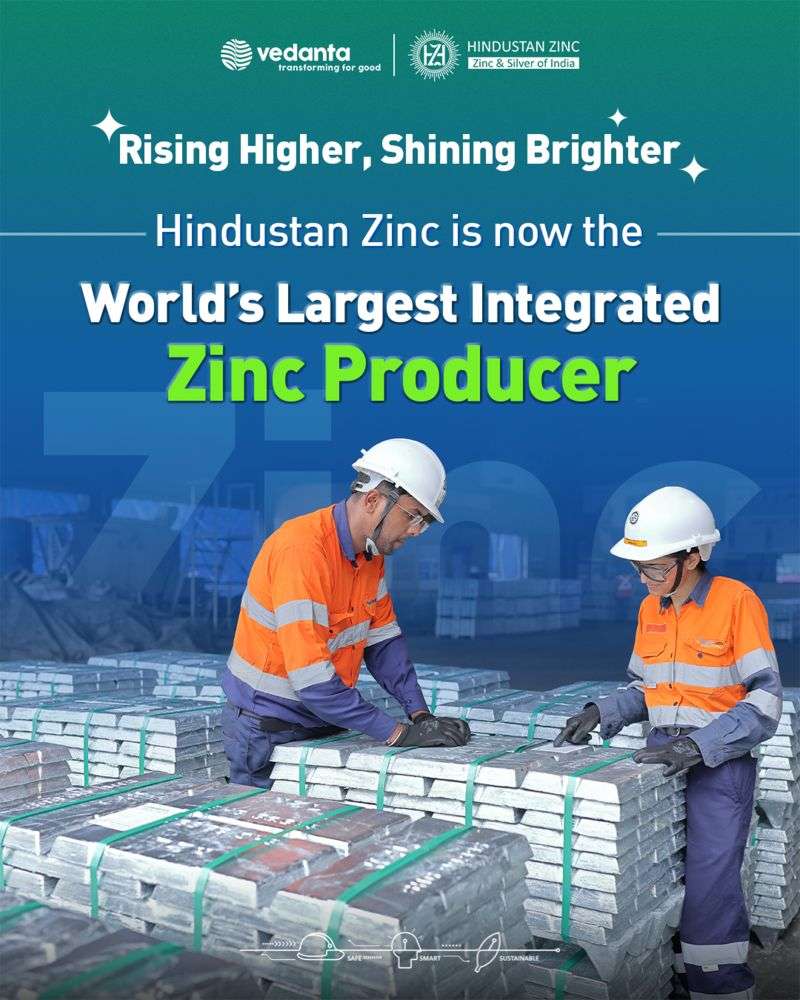
A Moment of Global Glory!
Hindustan Zinc is now the World’s Largest Integrated Zinc Producer! From reinforcing towering skyscrapers to driving cutting-edge innovations, zinc forms the backbone of modern progress and India now leads the world in producing this MetalForLife. With an unwavering commitment to excellence, sustainability, and technological advancement, Hindustan Zinc is proudly forging the path to an AmaZinc future!
metals mining manufacturing silver steel coatedsteel iron
What the eye misses, AI catches
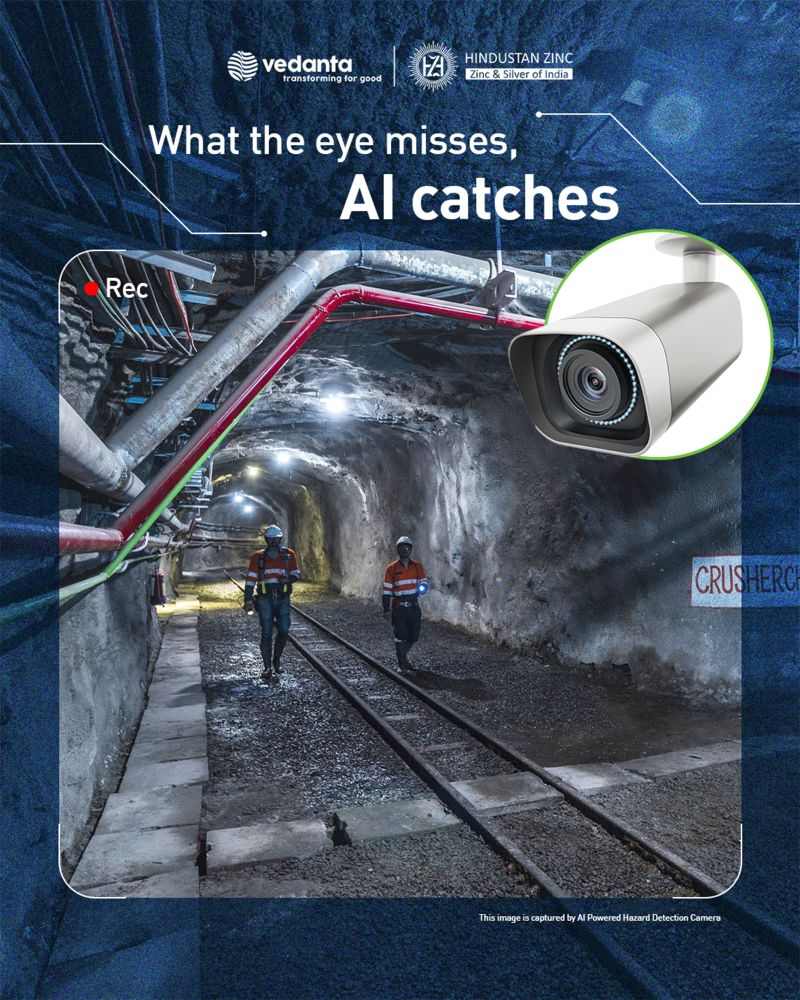
What the eye misses, AI catches
At Hindustan Zinc, safety is at the core of everything we do, and technology is our enabler. That’s why we’ve integrated Detect AI, a cutting-edge, highly advanced monitoring system that enhances workplace safety with intelligent, real-time surveillance. No blind spots, just smarter protection – because a safer workplace starts with sharper vision.
Zinc Silver Digitalisation Automation ArtificialIntelligence Innovation AI Advancements Manufacturing Metals Mining
Built to Last: Why Zinc is the Future of Stronger, Smarter Infrastructure
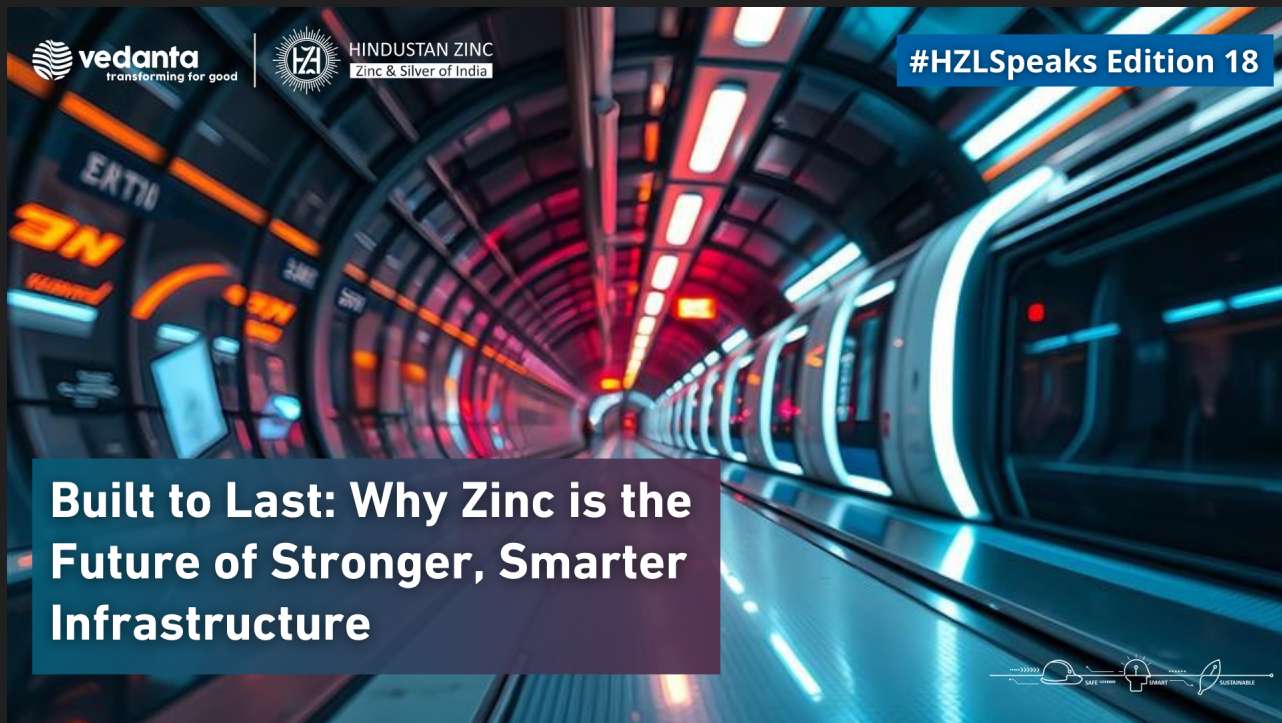
Built to Last: Why Zinc is the Future of Stronger, Smarter Infrastructure
Dear Readers,
If you’re planning a new home, upgrading a building, or designing large-scale public spaces, PAUSE! Here’s something you need to know first – your choice of material isn’t just about aesthetics; it’s about durability, efficiency, and long-term value. And that’s where zinc comes in. In this edition of #HZLSpeaks, we dive into the remarkable role of zinc in modern infrastructure and why it’s becoming the go-to material for the future – whether in roofing, cladding, or large-scale construction.
From railway platforms to metro stations across India, zinc is proving its strength every day. These high-traffic spaces demand materials that can withstand extreme weather, pollution, and constant use – without frequent repairs or replacements. Zinc’s self-sacrificial layer makes it corrosion-resistant, ensuring long-lasting performance even in the toughest environments. Its role extends beyond just buildings – it’s a critical component in bridges, tunnels, ensuring that urban landscapes remain resilient and efficient.
But it’s not just about endurance – zinc is also incredibly lightweight and flexible, making it perfect for modern, sleek designs in both urban infrastructure and private buildings. Even in a contemporary home facade, zinc delivers on both strength and style. Its ability to form into various shapes without compromising its integrity allows architects and engineers to push the boundaries of design, from intricate facades to curved surfaces that were once difficult to achieve with conventional materials.
And here’s the real game-changer: sustainability. Zinc is 100% recyclable, maintains its properties even after multiple recycling processes, and contributes to lower energy consumption by reducing the need for resource-intensive materials. It also helps regulate indoor temperatures, reflecting heat in the summer and retaining warmth in the winter, leading to significant energy savings over time. In large-scale urban developments, this means reduced environmental impact and improved energy efficiency across entire cityscapes. With the global push towards sustainable construction, zinc is emerging as the material of choice for builders, urban planners, and homeowners alike.
From your home to India’s biggest transportation hubs, Hindustan Zinc’s (the world’s second largest producer of integrated zinc) #MetalForLife – zinc is shaping the future of construction – strong, sustainable, and built to last, making every structure a step towards a smarter, #AmaZinc tomorrow.
Why is Aluminum preferred over Iron & Steel – And Why PFA’s Outshine SFA’s?
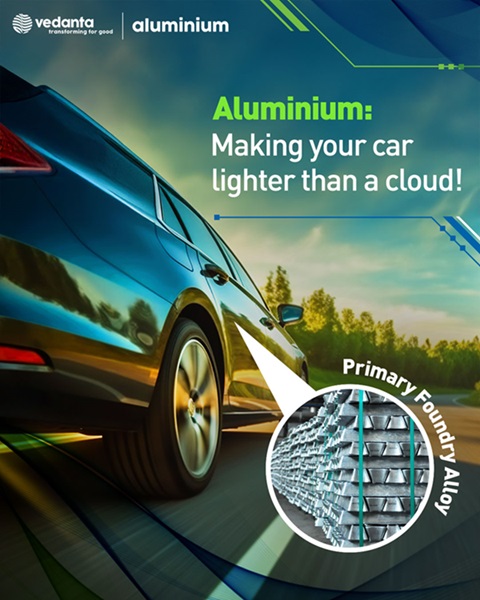
Why is Aluminum preferred over Iron & Steel – And Why PFA’s Outshine SFA’s?
Abstract:Aluminium alloys have revolutionized transportation and automotive industries due to their superior strength-to-weight ratio and excellent corrosion resistance compared to iron and steel. The transition to a greener economy and the rise of electric vehicles (EVs) have amplified the demand for lightweight, fuel-efficient, and sustainable materials. Among these, Primary Foundry Alloys (PFAs) are emerging as the material of choice for critical applications, offering unmatched purity and performance compared to Secondary Foundry Alloys (SFAs).
Technical Explanation
Why is Aluminium replacing Iron & Steel?
The push toward sustainability and energy efficiency is driving the adoption of aluminium alloys over traditional iron and steel:
- Lightweight for Fuel Efficiency: Aluminium’s lightweight properties reduce vehicle weight, significantly improving fuel efficiency in internal combustion engine (ICE) vehicles and enhancing the range of EVs.
- Corrosion Resistance: Aluminium’s natural resistance to rust ensures longer-lasting components, reducing maintenance and lifecycle costs.
- Design Flexibility: Higher silicon content and advanced casting techniques allow aluminium to be used in intricate, high-performance designs.
- Strength-to-Weight Ratio: Aluminium alloys provide comparable strength to steel at a fraction of the weight, making them ideal for lightweight, fuel-efficient transportation solutions.
Applications in the Automotive Industry
Aluminium castings have become integral to automotive engineering:
- Powertrains: Engine blocks, pistons, cylinder heads, manifolds, and transmissions.
- Chassis: Brackets, brake pads, suspension, steering components, and structural panels.
- Body Structures: Doors, bonnets, crossbeams, and other exterior attachments.
- Electric Vehicles (EVs): Battery casings and structural frames.
- Wheels: Cast wheels are a major consumer of aluminium foundry alloys.
PFA vs. SFA – The Key Differentiators
Aspect |
Primary Foundry Alloys (PFAs) |
Secondary Foundry Alloys (SFAs) |
Source |
Pure aluminium with alloying elements. |
Recycled scrap with some primary aluminium added. |
Impurities |
Lower impurity levels (<0.20% Fe for critical applications). |
Higher impurity levels, particularly iron. |
Applications |
Critical components requiring high ductility and strength. |
Non-critical components or pressure die casting. |
Cost |
Higher cost due to purity and production process. |
Lower cost, suitable for less demanding uses. |
Why PFAs Are Preferred
- Purity Matters: Critical applications like alloy wheels, engine block castings require iron levels below 0.20%, achievable only with PFAs.
- Enhanced Mechanical Properties: PFAs exhibit superior ductility, castability, and structural integrity, making them indispensable for stress-bearing automotive components.
- EV Growth Opportunities: As EV production scales, demand for PFAs in structural and battery components is set to rise due to their lower impurity levels and superior performance.
Easy example for better Understanding
Imagine building a house. You could use bricks made from pure, high-quality clay (PFAs) or bricks made from recycled materials mixed with impurities (SFAs). The pure clay bricks are stronger, more uniform, and better suited for critical parts of the house like the foundation or load-bearing walls. They ensure the house stands firm and lasts long.
On the other hand, the recycled bricks might be cheaper and okay for building a garden wall or a tool shed but aren’t reliable for the main structure because impurities can weaken them. Similarly, PFAs are the reliable choice for critical, high-performance auto parts, while SFAs are suited for simpler, less demanding applications.